Mga spotlight
Technician ng Kagamitan, Assembler ng Kagamitan, Technician sa Pagpapanatili ng Kagamitan, Operator ng Kagamitan, Inhinyero ng Kagamitan, Technician sa Paggawa, Espesyalista sa Fabrication, Assembler ng Mekanikal, Tagabuo ng Machine, Production Technician
Ang terminong "kagamitan" ay sumasaklaw sa libu-libong iba't ibang mga item na ginagamit sa hindi mabilang na mga industriya. Mga bulldozer, blender, monitor ng presyon ng dugo. Mga computer, car jack, dumbbells. Voltage tester, Bunsen burner, fire extinguisher...patuloy ang listahan.
Ang kagamitan ay ginagamit upang gumanap o tumulong sa lahat ng uri ng mga gawain at pag-andar. Karaniwan itong binili sa komersyo at “off-the-shelf,” ibig sabihin ay umiiral na ito at madaling bilhin. Ngunit kung minsan may mga gawaing kailangang gawin—at walang umiiral na kagamitan na idinisenyo upang gawin ang mga ito! Doon pumapasok ang mga Equipment Fabricator para iligtas ang araw.
Bilang isang proseso, ang katha ay nauugnay sa machining ngunit nagsasangkot ng higit pang paggupit, pagyuko, pagwelding, paggugupit, at pagbubuo ng mga piraso. Ang machining, sa kabilang banda, ay higit na umaasa sa paggiling, pag-ikot, pagbabarena, paggiling, at pagla-lathing.
Ang mga gawang kagamitan ay tumutukoy sa mga custom-made na device o tool na espesyal na nilikha para sa mga natatanging layunin. Maaaring kabilang sa mga naturang kagamitan ang mga customized na makina para sa mga layuning pang-industriya, mga espesyal na rig para sa paggawa ng pelikula, pinasadyang mga medikal na kagamitan, kagamitan sa pagsasaliksik at laboratoryo, mga pagbabago sa sasakyan, kagamitang pang-sports, atbp. Anuman ito, ang Mga Tagagawa ng Kagamitan ay laging handa sa hamon!
- Pagkuha sa disenyo, paggawa, at pag-assemble ng mga bagong kagamitan upang matulungan ang mga organisasyon na makamit ang kanilang mga layunin
- Posibleng gumawa ng isang bagay na magpapabago sa isang industriya
- Mga natatanging pagkakataon para sa pagpapaunlad ng mga kasanayan
Oras ng trabaho
- Gumagawa ang mga Tagagawa ng Kagamitan ng mga full-time na trabaho, karaniwan nang walang pasok sa mga gabi, katapusan ng linggo, at holiday, kahit na maaaring kailanganin paminsan-minsan ang overtime upang manatili sa iskedyul.
Mga Karaniwang Tungkulin
- Makipagkita sa mga tagapamahala o kliyente upang suriin ang kanilang mga kinakailangan para sa gawa-gawang kagamitan
- Brainstorm ideas for what such equipment might look like, its features, and the estimated cost of productionIf multiple pieces of equipment are needed, review manufacturing procedures and costs
- Gumawa o suriin ang mga nakasulat na paglalarawan o sketch, blueprint, teknikal na guhit, atbp.
- Sumang-ayon sa mga tuntunin ng trabaho, kabilang ang mga timeline at badyet
- Makipagtulungan sa mga miyembro ng koponan, kabilang ang mga inhinyero o consultant, kung kinakailangan
- Humiling ng mga kagamitan, kasangkapan, at hilaw na materyales na kinakailangan upang simulan ang trabaho
- Use hand tools and operate machines to fabricate workpieces. Assemble parts when ready
- Markahan ang mga linya ng pagputol sa mga materyales; suriin upang matiyak na ang mga piraso ay ligtas na nakakabit at nakahanay
- Suriin ang mga bahagi o panghuling produkto para sa katiyakan ng kalidad
- Magsagawa ng mga pagsubok sa stress at i-troubleshoot ang mga prototype upang matiyak na maayos ang paggana bago isumite ang mga ito para sa pagsusuri
- Kumuha ng feedback at gumawa ng mga pagsasaayos
Mga Karagdagang Pananagutan
- Dumalo sa mga pulong ng kagamitan/pagbuo ng produkto
- Sumunod sa mga pamantayan at alituntunin sa kaligtasan
- Gumawa ng mga detalyadong ulat ng lahat ng gawain
- Sumulat o tumulong sa pagsulat ng mga manwal sa pagpapatakbo para sa mga bagong kagamitan
- Manatiling up-to-date sa mga naaangkop na software at teknikal na manwal
- Magsanay at magturo ng mga bagong fabricator, machinist, operator, technologist, at technician, kung kinakailangan
- Panatilihing malinis ang mga lugar ng trabaho at magsagawa ng regular na pagpapanatili sa mga makina
Soft Skills
- Pagkaalerto
- Analitikal
- Maingat
- Kakayahan sa pakikipag-usap
- Nakatuon sa pagsunod
- Kritikal na pag-iisip
- Mabusisi pagdating sa detalye
- Disiplina
- Independent
- Layunin
- Organisado
- pasyente
- Pagpaplano at organisasyon
- Pagtugon sa suliranin
- Kaligtasan-kamalayan
- Mukhang makatarungan
- Stamina
- Pagtutulungan ng magkakasama
- Pamamahala ng oras
Teknikal na kasanayan
- Pagbabasa ng blueprint
- Welding / gawaing metal
- Machining and machinist programs such as Armchair Machinist and Machinists’ Calculator
- Computer-aided design programs like Autodesk AutoCAD, CATIA, PTC Creo Parametric, and SolidCAM
- Computer-aided manufacturing software like Autodesk Fusion 360 and CNC Mastercam
- Industrial control software such as EditCNC or Mazak Mazatrol
- Procedure management programs like Hexagon Metrology PC-DMIS
- Mga tool sa pagsukat ng katumpakan (caliper, micrometer, at gauge)
- Kaalaman sa mga materyales at mga katangian ng mga ito (kabilang ang iba't ibang uri ng metal at metal na haluang metal tulad ng bakal, tanso, aluminyo, tanso, sink, tingga, vanadium, at manganese)
- Pamilyar sa mga tool at kagamitan gaya ng welding machine, gunting, press, grinder, CNC machine, laser, plasma cutter, waterjet, panukat na instrumento, at safety gear
- Familiarity sa hydraulic system, electrical wiring, lubricants, at baterya
- Mga pamamaraang pangkaligtasan at pangunang lunas
- Industriya ng aerospace
- Agribusiness
- Industriya ng sasakyan
- Paggawa ng kompyuter at elektronikong produkto
- Mga kumpanya sa konstruksyon
- Industriya ng pagproseso ng pagkain
- Paggawa ng makinarya
- Mga kumpanya ng langis at gas
- Sektor ng nababagong enerhiya
- Pananaliksik at pag-unlad
- Pansamantalang mga serbisyo ng tulong
- Paggawa ng kagamitan sa transportasyon
Ang mga fabricator ng kagamitan ay dapat magpanatili ng mataas na antas ng katumpakan at maghatid ng mga de-kalidad na prototype at mga natapos na produkto na nakakatugon sa mga inaasahan ng kanilang employer o kliyente. Ang trabaho ay dapat gawin nang ligtas, sa loob ng mga itinakdang timeframe at badyet, at alinsunod sa mga naaangkop na pamantayan ng industriya.
Ang napakaraming kahilingang ito ay naglalagay ng maraming panggigipit sa mga fabricator, na ang trabaho ay lubos na sinisiyasat. Kapag nahuli ang mga bagay sa iskedyul, maaaring kailanganin nilang maglagay ng dagdag na oras para makahabol. Ito ay isang pisikal na hinihingi na trabaho, na kinasasangkutan ng pag-aangat, matagal na pagtayo, at pagkakalantad sa iba't ibang mga panganib—na lahat ay maaaring makapinsala sa paglipas ng panahon.
Trends in the field of equipment fabrication include the rise of Industry 4.0, which uses technologies like automation, artificial intelligence, Cyber-Physical Systems, cloud computing, 3D printing, and the Internet of Things to improve efficiency and productivity.
For equipment that will be mass-produced, the Industrial Internet of Things enables manufacturers to connect machines, devices, and sensors to the Internet. This allows real-time data collection, helping to optimize operations. Sustainable Manufacturing is another growing trend, as companies seek to reduce waste, improve energy efficiency, and utilize renewable resources. However, this may be less important for customized equipment that will only be made once or a few times.
Ang mga Fabricator ng Kagamitan ay nasisiyahan sa pag-visualize ng mga ideya at paggamit ng kanilang mga kamay upang bigyang-buhay ang mga ito. Kumportable silang gumamit ng mga kasangkapan at nakatigil na mabibigat na kagamitan. Maaaring nasiyahan sila sa mga klase sa matematika at tindahan sa paaralan, pati na rin ang disenyo at computer programming.
Para sa kanila, madaling makipagtulungan ngunit hindi nila iniisip na magtrabaho nang mag-isa sa mahabang panahon kung saan maaari silang tumuon sa gawaing nasa kamay. Maaaring sila ay lubos na independiyenteng paglaki, at sa gayon ay pakiramdam na tama sila sa pagkumpleto ng mga proyekto nang walang isang toneladang pakikipag-ugnayan sa iba.
- Ang mga Tagagawa ng Kagamitan ay nangangailangan ng hindi bababa sa diploma sa mataas na paaralan o GED
- Maraming manggagawa sa larangang ito ang kumukuha ng sertipiko o associate's degree sa isang community college o technical school para matuto o mag-ayos sa:
- Math
- Pagbabasa ng blueprint
- Welding / gawaing metal
- Ligtas na paggamit ng hand tool
- Mga programang CAD/CAM
- Paano patakbuhin ang mga CNC machine
- Ang iba pang karaniwang mga kurso ay kinabibilangan ng:
- Mga Proyektong Aluminyo
- Baluktot
- Notching
- Pagbuo at Pagbuo ng Bahagi
- Mga Operasyon ng Mill at Lathe
- Sheet Metal Shaping
- Pagputol ng Plasma
- Sponsored apprenticeships or internships are another way to get training, so include those keywords when searching for job posts online
- Fabricators can also learn their skills via specialized programs like those from The Fab School. Check out related course offerings from Coursera, too!
- Maaaring ipakita ng mga opsyonal na programa sa sertipikasyon ang pangako ng mga Tagagawa ng Kagamitan sa kalidad, tulad ng:
- Ang mga Tagagawa ng Kagamitan ay hindi kailangang pumasok sa isang apat na taong unibersidad. Ngunit ang isang sertipiko o kasama sa isang teknikal na paaralan o kolehiyo ng komunidad ay magiging kapaki-pakinabang
- Isaalang-alang ang halaga ng matrikula, mga diskwento, at mga oportunidad sa lokal na iskolarship (bilang karagdagan sa tulong na pederal)
- Isipin ang iyong iskedyul at kakayahang umangkop kapag nagpapasya kung mag-e-enroll sa isang on-campus, online, o hybrid na programa. Maraming nauugnay na kurso ang kailangang gawin nang personal para makakuha ng hands-on na karanasan
- Suriin ang mga istatistika ng paglalagay ng trabaho ng programa para sa mga nagtapos
- Mag-sign up para sa maraming math, physics, computer science, materials science, at shop class sa high school
- Isaalang-alang ang pag-aaral tungkol sa mechanical drawing at blueprint reading sa pamamagitan ng self-study
- Take ad hoc classes online, from Coursera, Udemy, or other sites
- Mag-enroll sa isang community college o vocational/technical school program para matutunan ang mga pamamaraan ng fabrication, welding, CAD/CAM, CNC machining, atbp.
- Knock out a certification program such as AISC’s Certified Fabricator or AWS Certified Welder
- Makilahok sa isang fitness program na maaaring bumuo ng iyong lakas at tibay
- Makakuha ng ilang real-world na karanasan sa trabaho sa pamamagitan ng mga part-time na trabaho o internship na nauugnay sa paggawa o trabaho sa tindahan
- Request to do an informational interview with a working Equipment Fabricator to learn about their jobs
- Subaybayan ang mga contact na maaaring magsilbing mga sanggunian sa trabaho sa hinaharap
- Mag-aral ng mga libro, artikulo, at video tutorial na nauugnay sa tradisyonal at modernong mga proseso, tool, at kagamitan sa paggawa
- Makilahok sa mga online na forum upang magtanong at matuto mula sa mga batikang pro
- Makipag-ugnayan sa mga propesyonal na organisasyon upang matuto, magbahagi, makipagkaibigan, at mapalago ang iyong network (tingnan ang aming listahan ng Mga Mapagkukunan > Mga Website)
- Simulan ang paggawa ng resume nang maaga. Panatilihin ang pagdaragdag dito habang nagpapatuloy ka, para hindi ka makaligtaan ng anuman
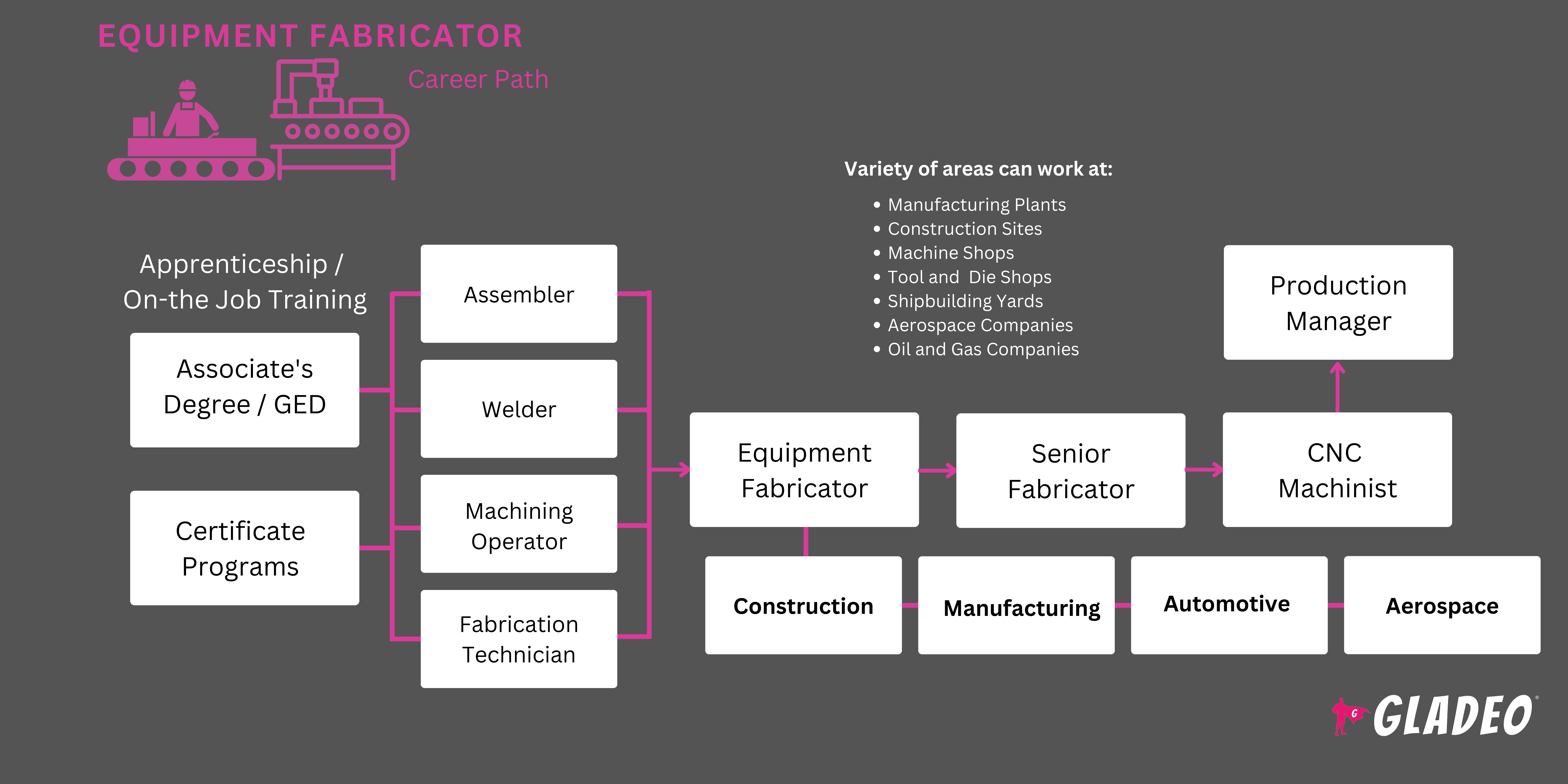
- Tingnan ang mga portal ng trabaho tulad ng Indeed.com , LinkedIn , Glassdoor , Monster , CareerBuilder , SimplyHired , o ZipRecruiter
- Look on Craigslist for job postings from smaller local companies
- Gumawa ng listahan ng mga lokal na kumpanya sa pagmamanupaktura ng kagamitan at bisitahin ang mga page ng karera ng kanilang mga website nang madalas
- I-advertise ang iyong mga serbisyo online, gaya ng sa LinkedIn o sa pamamagitan ng isang website
- Seek out apprenticeships or internships sponsored by employers, unions, or trade associations
- Magtanong sa isang working Equipment Fabricator para sa mga tip sa paghahanap ng trabaho
- Bisitahin ang career center ng iyong paaralan para sa tulong sa paghahanap ng mga job fair, pagsulat ng resume, at pagkonekta sa mga recruiter
- Manatiling nakikipag-ugnayan sa mga kaklase at gamitin ang iyong network para makakuha ng mga tip sa trabaho. Karamihan sa mga trabaho ay matatagpuan pa rin sa pamamagitan ng mga personal na koneksyon
- Tanungin ang iyong mga instruktor, dating superbisor, at/o mga katrabaho kung handa silang magsilbi bilang mga personal na sanggunian. Huwag ibigay ang kanilang personal na impormasyon sa pakikipag-ugnayan nang walang paunang pahintulot
- Check out some Equipment Fabricator-related resume examples and sample interview questions
- Practice doing mock interviews and learn how to dress appropriately for interviews
Master ang iyong kasalukuyang trabaho ngunit ipaalam sa iyong superbisor na interesado ka sa pag-unlad ng karera. Ipahayag ang iyong pagpayag na kumpletuhin ang karagdagang pagsasanay
- Pag-aralan ang mga manwal sa pagpapatakbo ng kagamitan at software at maging bihasa sa mga tool na iyong ginagamit
- Makipagtulungan nang mabuti sa iba at makipag-usap nang malinaw at tapat tungkol sa mga detalye ng isang proyektong itinalaga sa iyo. Kung may hamon, ipaliwanag ito at subukang mag-alok ng mga solusyon
- Tiyakin na ang mga proyekto ay pinananatili sa iskedyul at nasa badyet
- Subaybayan ang fabrication, welding, at machining trend at advancements
- Consider specializing and getting advanced certifications in a challenging area, such as gas tungsten arc or laser hybrid welding
- Para sa mga nagtatrabaho sa mas maliliit na organisasyon, maaaring kailanganin mong mag-apply para magtrabaho sa mas malaki o ibang uri ng organisasyon para makakuha ng mas malaking suweldo o maabot ang mas matataas na layunin sa karera
- Makakatulong din ang pagkumpleto ng mga advanced na third-party na certification. Kasama sa mga opsyon ang:
- Certified Fabricator ng AISC
- AWS Certified Welder
- Certified Composite Technician
- Sertipikadong Robotic Arc Welding
- National Institute for Metalworking Skills certifications
- Ang Certified Metal Fabricator ng NCCER
- Ang Certified Manufacturing Technologist ng SME
- Ang isang bachelor's sa mechanical engineering o isang kaugnay na larangan ay maaaring magbukas ng karagdagang mga pagkakataon sa karera at magbigay ng mas malalim na pag-unawa sa mga prinsipyo ng engineering, agham ng materyales, at mga konsepto ng disenyo
Mga website
- American Composites Manufacturers Association
- American Foundry Society
- American Institute of Steel Construction
- American Machine Tool Distributor' Association
- American Society of Mechanical Engineers
- American Welding Society
- Asosasyon ng mga Fabricator at Manufacturers, International
- IPC
- International Association of Sheet Metal, Air, Rail, and Transportation Workers (SMART)
- National Center for Construction Education and Research (NCCER)
- National Institute for Metalworking Skills
- National Tooling and Machining Association
- Precision Machined Products Association
- Society of Manufacturing Engineers (SME)
Mga libro
- Composite Material Fabrication Handbook #1, by John Wanberg
- Learn to Weld: Beginning MIG Welding and Metal Fabrication Basics, by Stephen Christena
- Sheet Metal Workers Pocket Manual, by Fred Schumacher and Calude Zinngrabe
- Welding for Beginners: The Secrets To Welding, Cutting, and Shaping Metal Like a True Professional, by Cosmo Castro
Ang Equipment Fabricator ay maaaring maging isang napaka-kapaki-pakinabang na pagpipilian sa karera! Ito ay puno ng mga pagkakataong gumawa ng malikhaing gawain gamit ang iyong mga kamay, na gumagawa ng mga custom na piraso ng kagamitan upang matulungan ang mga employer o kliyente na malampasan ang mga hamon at maabot ang kanilang mga layunin. Ngunit kung ito ay mukhang hindi tama para sa iyo, narito ang ilang mga kaugnay na trabaho na dapat isaalang-alang:
- Istraktura ng Sasakyang Panghimpapawid, Mga Ibabaw, Rigging, at Assembler ng Sistema
- Boilermaker
- Coil Winder, Taper, at Finisher
- Electrical at Electronic Equipment Assembler
- Electromechanical Equipment Assembler
- Engine at Iba pang Machine Assembler
- Fiberglass Laminator
- Industrial Machinery Mechanic
- Manggagawa ng bakal
- Manggagawa sa Pagpapanatili ng Makinarya
- Metal at Plastic Machine Worker
- Millwright
- Sheet Metal Worker
- Structural Metal Fabricator at Fitter
- Timing Device Assembler
- Welder
Newsfeed
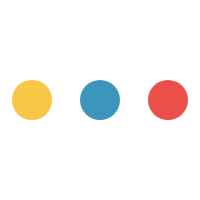
Mga Tampok na Trabaho
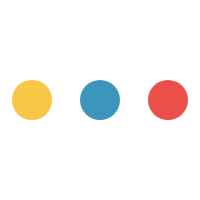
Mga Online na Kurso at Tool
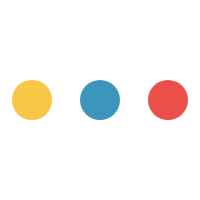
Annual Salary Expectations
New workers start around $37K. Median pay is $40K per year. Highly experienced workers can earn around $49K.